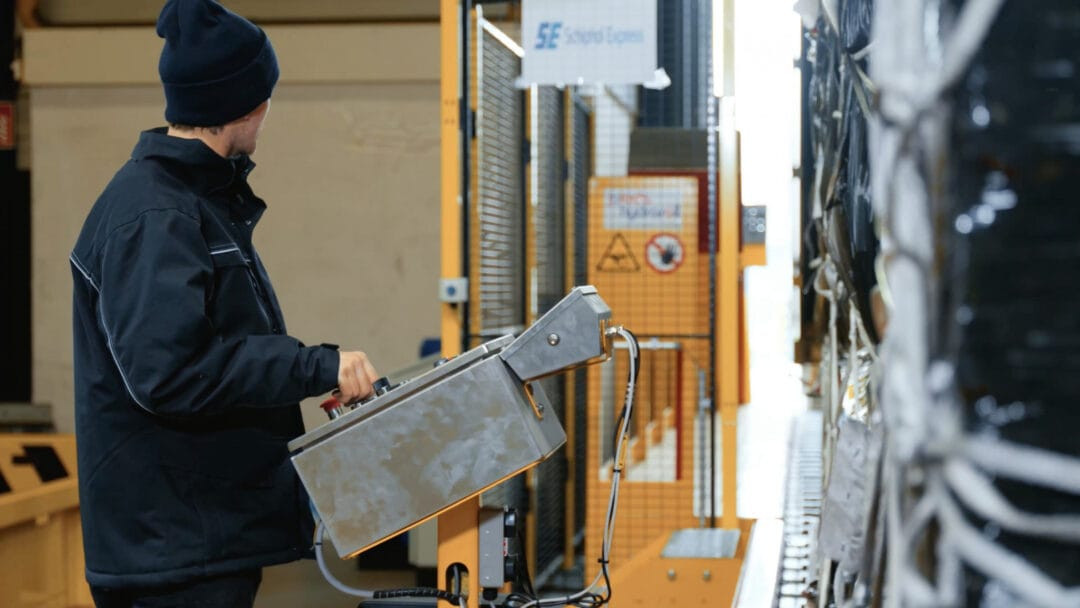
Joloda Hydraroll has installed the automatic cargo processing system for the Schiphol Airport in the SCIPHOL Airport to make a loading and unloading trailer faster and more efficient. It is one of the first major facilities under the new Joloda Air Carraine Division, which was launched in 2024.
Schiphol Express provides comprehensive logistical services, including goods processing, temporary ULD storage, sorting, transportation for charging, airlines, and logistics service providers.
The company operates from Schiphol and Eindhoven airports, and the company runs the entire logistical process, from loading and unloading goods in the first line warehouses to transport and delivery across the Netherlands.
To deal with increasing sizes, the Schiphol Express needed a more efficient and reliable solution that speeds the transportation of trailer shipments between its trucks and warehouse.
Challenge: Hand operations consumed for time
The current equipment of the Schiphol Express was old and needed to replace it with a modern version of the latest technology. The manual emptying of air cargo, such as Usds and PMC, was a time consuming and work density, which leads to long transformation times in the trailer and high employment costs.
The company requested a system to simplify operations, reduce the risk of manual dealings, and enhance total efficiency when transporting air cargo between trailers and warehouses.
Solution: Joloda Hydraroll air shipments equipment
Joloda Hydraroll is designed, manufactured and installed a fully integrated system consisting of a 20 -foot truck berth and two parking -long situations. The Schiphol Express composition allows to prepare or unload a full truck load (four 10 feet sites) more efficiently.
The truck cage system is characterized by hydraulic height and side adjusting to accurately align the trucks to accuracy. Its height allows 20 feet to empty the PMC platforms 10 feet or one platform 20 feet from the trailer simultaneously. Once the platforms reach the end of the truck’s berth, the operator reduces the tube cage to comply with the veil system that is powered.
The truck berth is also determined using Winch, which allows the withdrawal of air cargo from trailers in cases where the platforms stumble, even if the trailer is equipped with the air cylinder, systems with normative swirls, or energy -powered cargo balls. Since all air charging trailers are equipped with a minimum registration, Winch is a backup copy to ensure smooth operations.
In addition, the discovery of the trailer was combined into the truck’s cage. The system is automatically discovered when properly trailer and ready to receive charging, which improves efficiency and safety.
The Rollerbed system, which operates, consists of two places of 10 feet -pairing surveyors with the truck berth to ensure the entire system operates as a single smooth unit. Once the sidewalk is aligned with the energy -powered roller, its automatic rollers are pushing the air merchandise to the warehouse, eliminating manual interaction and speeding up the workflow. The system is also equipped with weight scales, allowing air cargo to be evaluated and described as a printed poster before further treatment.
Automation plays a major role in making this one -person process. PhotoCell automatically closes the engines to prevent the pushing of air cargo to the length of the truck berth or the subsidized rotational system, ensuring that it is dealt with monitoring and effective charging at all times.
Results: Emptying a whole truck in minutes
The team in the Schiphol Express has increased productivity and operational cost reduction since the implementation of the new air freight processing system; Automation of the discharge process has reduced discharge times to just minutes for each truck load.
The operators also noticed a smoother workflow, and the ability to deal with higher charging sizes has improved service levels for customers. Strong construction guarantees durability under high demand conditions, while normative design and smooth complementarity with current logistical processes are reinforced by the effectiveness of installation and the opportunity to expand in the future with the growth of charging sizes.
“The installation of the processing of air cargo equipment has transformed our operations. The automatic system has greatly reduced the loading and unloading of the trailer, improving the efficiency of the workflow, and reinforced safety for our team.
“The device has been combined with our current operations smoothly, allowing us to deal with high -reliability sizes with greater reliability. This investment will be effective in improving our logistical capabilities and performance.”
conclusion
By installing Joloda Air Cargo Handling Truck and Rollerbed, the Schiphol Express improved air cargo processes. This solution contains workflow flows, improving efficiency, and reducing operational costs, which enhances the Schiphol Express position as a leader in air charging logistics.